Bollore Logistics (18 May 2021) - Problem Statement (3)
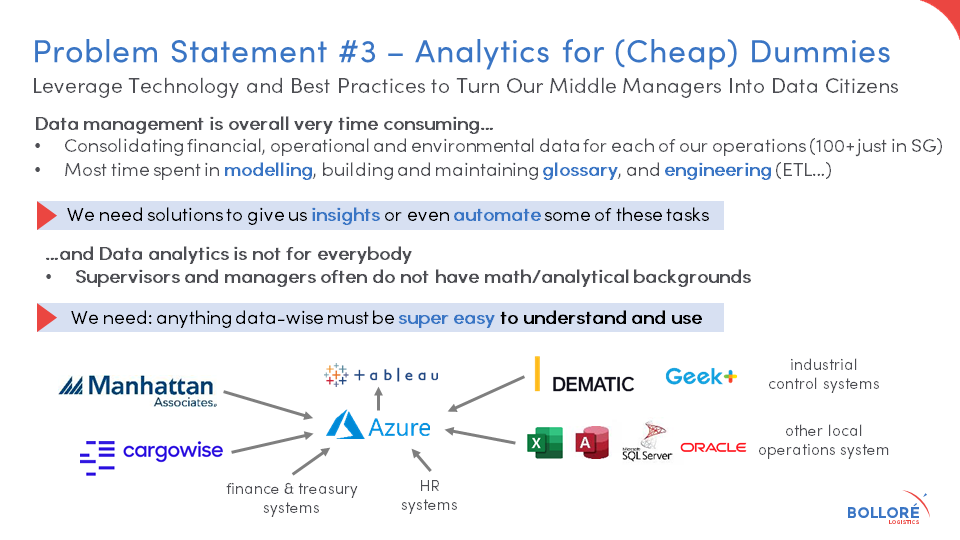
Technology and best practices to turn our middle managers into data citizens.
For startups with Technology Readiness Levels of 4 & above.
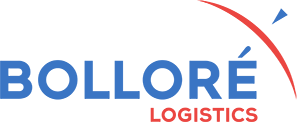
Technology and best practices to turn our middle managers into data citizens.
For startups with Technology Readiness Levels of 4 & above.
Perfect low-code platforms to capture more relevant data and improve efficiency.
For startups with Technology Readiness Levels of 4 & above.
Objectives:
Desired Outcomes:
Current Limitations:
Objectives:
Desired Outcomes:
Current Limitations:
Objectives:
Desired Outcomes:
Current Limitations:
Objectives:
Desired Outcomes:
Current Limitations:
Objective:
Desired Outcomes:
Current Limitations:
A platform to synchronise different transportation, yard & warehousing systems to optimise resources & unlock efficiency with speed.
For early-stage startups with robust solutions & readiness to grow with Unilever.
Solutions that consider customer demands that may change rapidly (such as delivery destination, delivery window) to improve logistics efficiency.
For early-stage startups with robust solutions & readiness to grow with Unilever.
Objective:
Desired Outcomes:
Current Limitations: