Content
Objective:
- To improve the transfer efficiency of robot painting.
Desired Outcomes:
- To improve efficiency by 30% through optimisation of the robot programme and spray parameters using vision system based AI/ML logic:
- The vision system fitted on the robot scans the painting jig and captures the image of the parts to be painted.
- Robot path to be generated using AI/ML algorithm based on the image data captured by the vision system.
Current Limitations:
- Two-wheeler parts are painted using a robot painting process, with the parts moving on a conveyor.
- Robot programme and spray parameters are developed by trial and error process based on the shape of the parts to be painted.
- It is an iterative process of modifying robot parameters and checking the paint film built on the parts after baking.
- This results in lower paint transfer efficiency – paint transfer efficiency is the ratio of paint deposited on the part to the total paint sprayed.
- Transfer efficiency for parts is measured by weight method, i.e. weight of the paint on the component to the total paint sprayed from the robot gun.
- The above process is highly skill-oriented (a skilled robot programmer is needed)
- Wide variety of parts to be painted in a single paint plant.
- Robot programmes cannot be optimised for each type of part, as it is a manual process of creating the robot programme.
- Trials and verification are time-consuming as paint thickness can be checked only after parts are baked in the oven.
- High skill requirement for engineers carrying out robot teaching for the painting process.
Heading
Improvement of Paint Transfer Efficiency
Logo
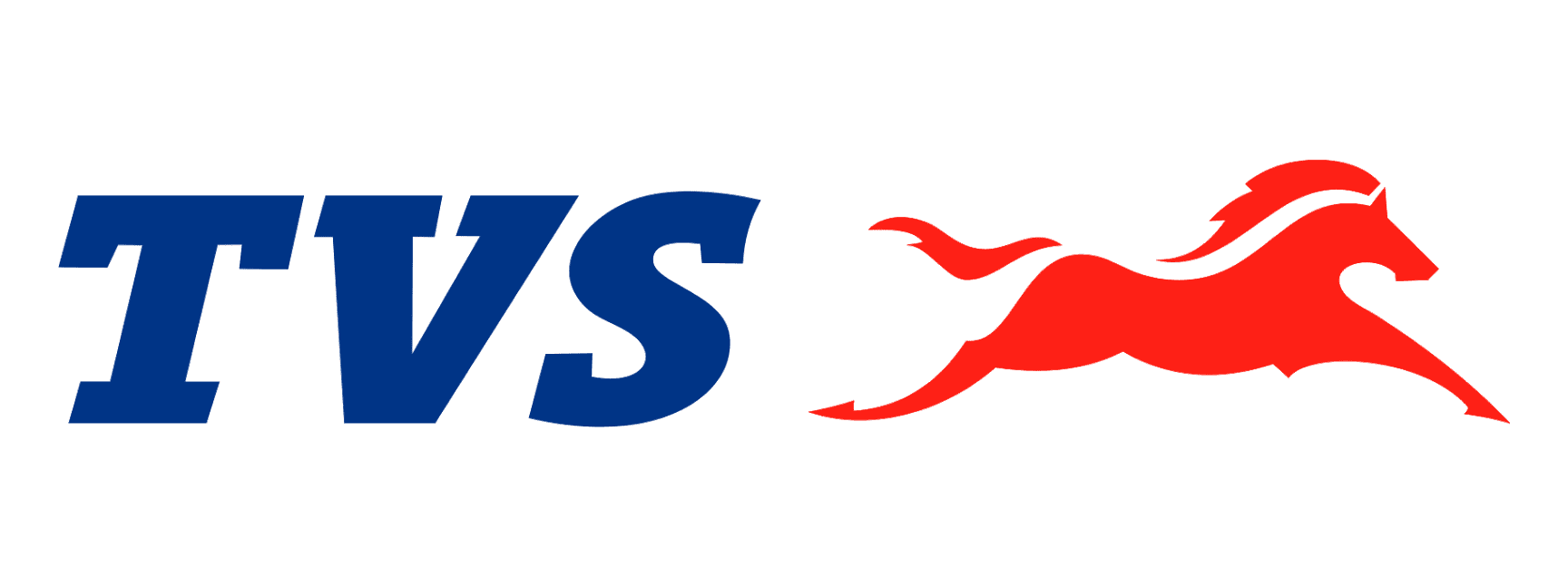
Category
Industry
CTA Text
COMPLETED
Sort Order
2